Design, Development
& Engineering
The Bonastre difference. The main attributes that drive our engineering and make us unique.
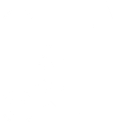
LEADING R+D+I
SYSTEM
Certified R+D+I management system (UNE 166002) powered by the most robust fully automated Technology Forecasting and Competitive Intelligence system.

EXTENSIVE
KNOW-HOW
Our diverse skills, expertise, and knowledge across various medical domains empower us to create effect designs and innovate solutions.

DESIGN FOR MANUFACTURING & ASSEMBLY
Our unmatched DFM and DFA expertise ensures seamless alignment of design and manufacturing, expediting industrialization and significantly reducing Time to Market.
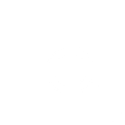
OPTIMIZED DESIGN APPROACH
We meticulously craft manufacturing drawings through our integrated engineering and manufacturing teams, prioritzing the optimal balance of Quality, Functionality, and Cost.
Contract Design & Development Services
We offer a comprehensive range of medical device design and development services to transform your idea from concept phase to the production of a market-ready product. With our expertise and proven engineering practices, we ensure that your vision becomes a reality while accelerating your time to market and minimizing costs and technical risks.
Our Design & Development process is designed to cover the complete medical device lifecycle phases and is fully aligned with medical device regulation and standards:
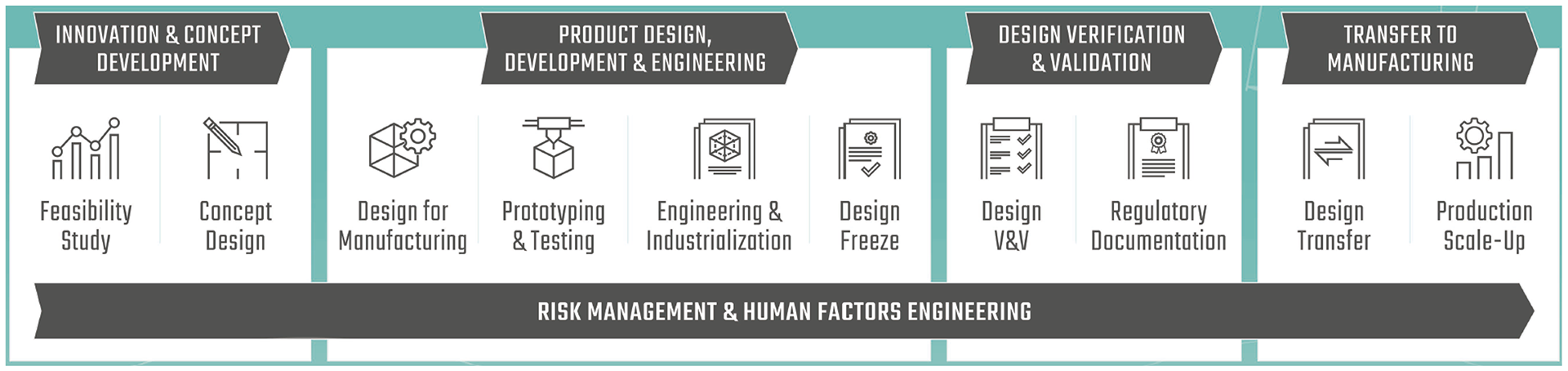
& Concept Development
Development & Engineering
& Validation
& Concept Development
1

Feasibility Study
- Clinical Need Investigation
- Market Research & Competence Analysis
- IP Landscaping
- Regulatory Overview
- Commercial Feasibility
2
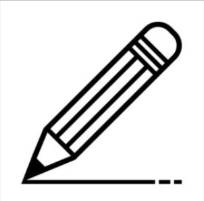
Concept Design
- User Needs Definition
- Technological Survillance
- Concept Sketches
- 3D CAD Renders
- Physical Mockups & Concept Models
- Proof of Concept Testing
Development & Engineering
1

Design for Manufaturing
- Technical Coordination
- Product Requirements
- Detailed Design Drawings & 3D Models
- Materials Characterization
- Tolerance Analysis
- Simulation and Finite Element Analysis
- Reverse Engineering
2

Prototyping & Testing
- Testing Plan Definition
- Rapid Prototyping
- Pilot Prototyping
- Prototype Testing
- Design Iteration Process
- Test Method Development
3
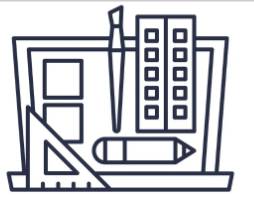
Engineering & Industrialization
- Industrial Design
- Detailed Production Drawings
- Tooling Design
- Materials Selection
- Suppliers Selection
- Industrial Prototyping
4
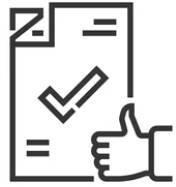
Design Freeze
- Product Specifications (Design Outputs)
- Packaging Design
- Instructions for Use
- Labelling Definition
- Design Freeze
& Validation
1
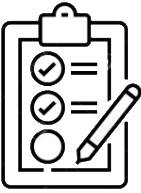
Design V&V
- V&V Testing Plan
- Benchtesting
- Custom testing Design
- Summative Usability Testing
- Testing Protocols
- Testing Reports
2
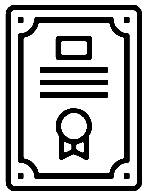
Regulatory Documentation
- Design History File
- Technical Documentation Support
- Batch Release Inspection Requirements
1

Design Transfer
- Device Master Record
- Bill of Materials
- Process Flowchart
- Manufacturing & Quality Instructions
- Equipment Calibration
- Process Validation
2
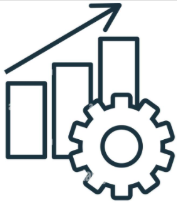
Production Scale-Up
- Regular Manufacturing
- Quality Control
- Product Assembly
- Cleaning & Packaging
- Finishing/Surface Treatments
1

Risk Management & Human Factors Engineering
- Risk Management Plan
- Hazard Analysis
- Design FMEA
- Application FMEA
- Process FMEA
- Risk Management Report
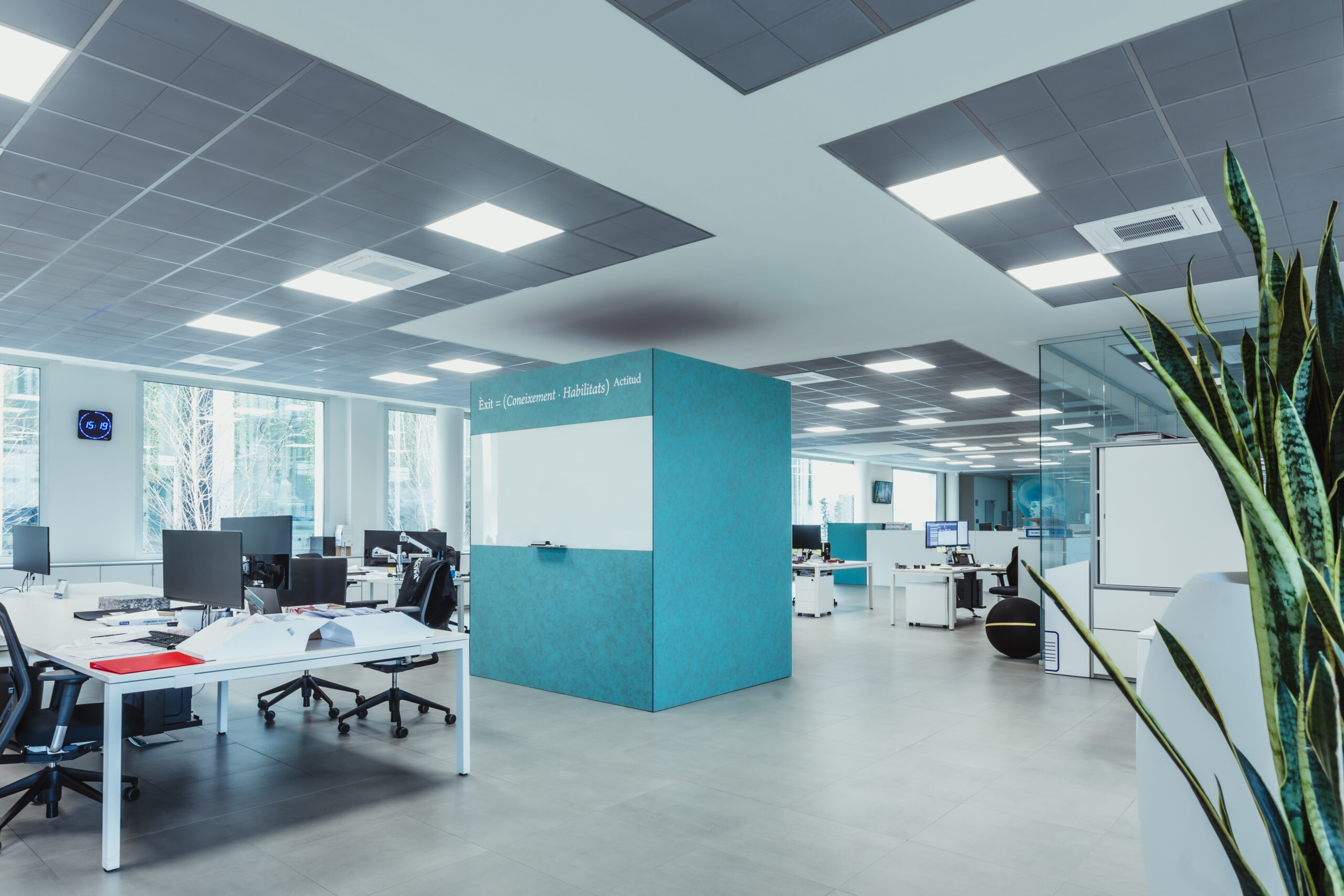
Innovation & Concept Development
We can assist you in transforming your initial ideas into viable and innovative solutions.
Our process begins with a comprehensive feasibility study. We analyze the market, assess technical challenges, and conduct regulatory and IP reviews to determine the viability of your idea.
After the initial study, our talented designers and engineers use a deign thinking approach to advance the concept design phase. We develop detailed concepts that meet user needs and are technologically feasible, ensuring your project’s success from the outset.
Product Design, Development & Engineering
Our expertise in design, development and engineering enables us to transform conceptual prototypes into detailed and industrialized designs. Through our exceptional Design for Manufacturing (DFM) and Design for Assembly (DFA) practices, we meticulously craft manufacturing drawings of the highest standards, where our high quality is born.
The implemention of rigorous Design Controls finalizes the design, ensuring top quality and facilitating seamless transition to industrialized production, which significantly reduces Time to Market.

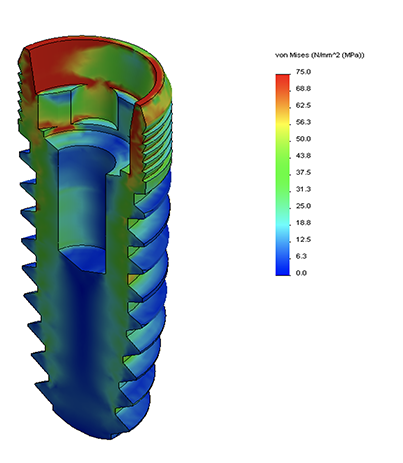
Finite Element Analysis
With cost-effective FEA services, we use advanced simulation sofware to predict, optimize, and validate designs, streamlining the process, reducing the need for numerous prototypes, and cutting testing costs. Optimize your design journey with precision and affordability.
Risk Management (ISO 14971)
We consistently integrate Risk Management into design and manufacturing right from the start, ensuring that final products meet essential safety controls and effectiveness. Employing robust risk management tools, we systematically evaluate, control, and reduce identified risks.
Human Factors Engineering (IEC 62366)
We specialize in developing user-friendly components and products, prioritizing usability, safety, and enhanced functionality. Our human factors and usability engineering approach is dedicated to meeting user needs and elevating safety standards.
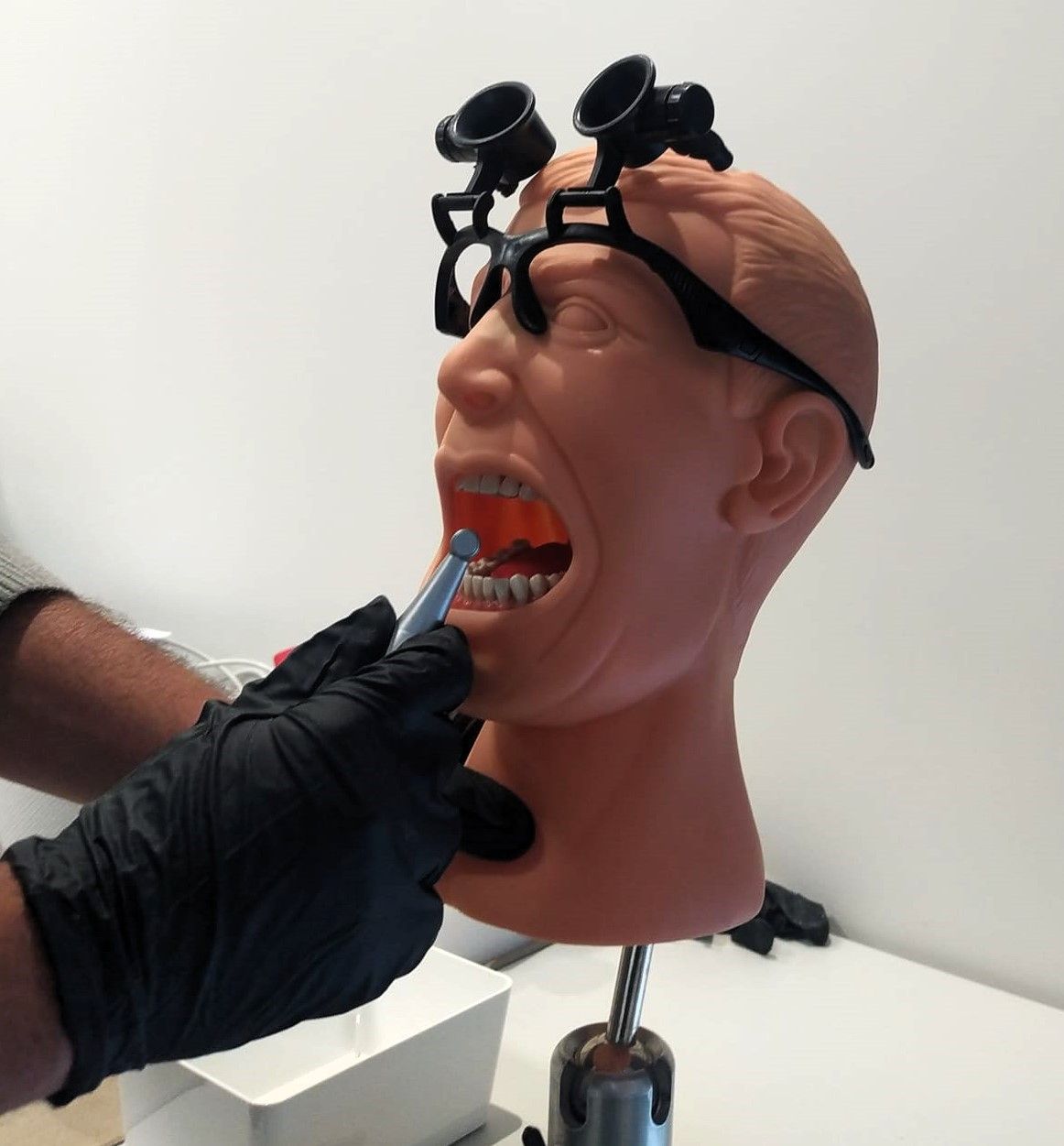

Design V&V Testing
Once the Design is frozen, we conduct V&V Testing with the purpose of:
- Validate that the design outputs (product specifications) align with the initial design inputs (product requirements).
- Verify that the product fulfills the user needs and intended purpose effectively.
- Ensure the safety and efficacy of the product.
Regulatory Documentation Support
We support you throughout the regulatory process, ensuring that the design and development process results in a comprehensive documentation package suitable for regulatory submissions and transition into commercial production.
Design Transfer & Production Scale-Up
We bridge the gap between design and manufacturing by offering comprehensive design transfer services. During this stage, our R&D and Manufacturing teams collaborate to ensure that design outputs are meticulously structured and documented into the Device Master Record (DMR), facilitating a smooth transition into manufacturing.
Furthermore, we provide scalable manufacturing and assembly services to accommodate projects of different volumes, meeting the needs of both low-volume and high-volume production requirements.
